
State-of-the art facilities materialize productivity and top-class quality.
- The raw materials and pigment are blended, and then (gelled by applying heat) the batch is kneaded by the thermoplastic heated large mixer.
Through the rotation control operation of the mixer at this time, we make it possible for plasticization of various materials.
(2 lines of large mixers, 1 line of auxiliary mixer)
- The gelled material is heated, keeping it at a temperature suitable for the next processing step.
In addition, a process eliminating fine foreign matter using a strainer (material filtration machine) helps prevent possible product contamination.
(2 Lines Each)
- After filtration in Step 2, the heated material is pressed by four temperature controlled rollers into a sheet.
To ensure precision machining temperature management, oil is used for heat mediation, enabling the stable processing of various materials in our facilities.
(2 Lines)
- The material is formulated with a foaming agent, and then by applying heat with a gas burner, it is possible to create a cushion effect in the material . This will also lead to weight reduction of the product and is cost effective, by suppressing the amount of material in proportion to the product thickness.
Subsequently rolled up and to cut to the desired finished product. (1 Line)
- Bonded by heat welding without using an adhesive sheet produced by the above process.
The sheet is made in various combinations such as: colored layer, foam layer, printing film, and based cloth.
Also, at the same time, an embossing process can be done on the seat itself. Wound up, merchandised as cut goods. (5 Lines)
- Sheets bonded together are pressed in a continuous winding finish to make a 3D shape.
These mats are primarily used for automobiles. (1 Line)
- Quality control systems to check the products of the above-mentioned equipment. With the testing of enhancement and measurement equipment corresponding to various fields of products.
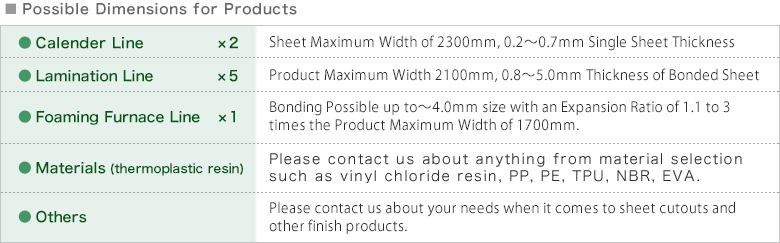
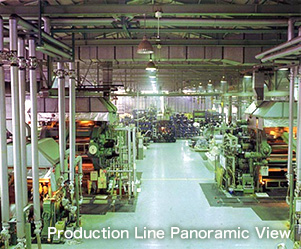

Experience accumulated over many years and cutting-edge technology.
Daidokasei is always pursuing innovated production systems.

•Reversed L-Shaped 28 inch Calender 1 Machine
•Z-Shaped 32 inch Calender 1 Machine
•Lamination Line 5 Machines
•Foam Furnace 1
•Continuous Vacuum Molding Machine 1
•Press Punching Machine 1 large, 1 small sized